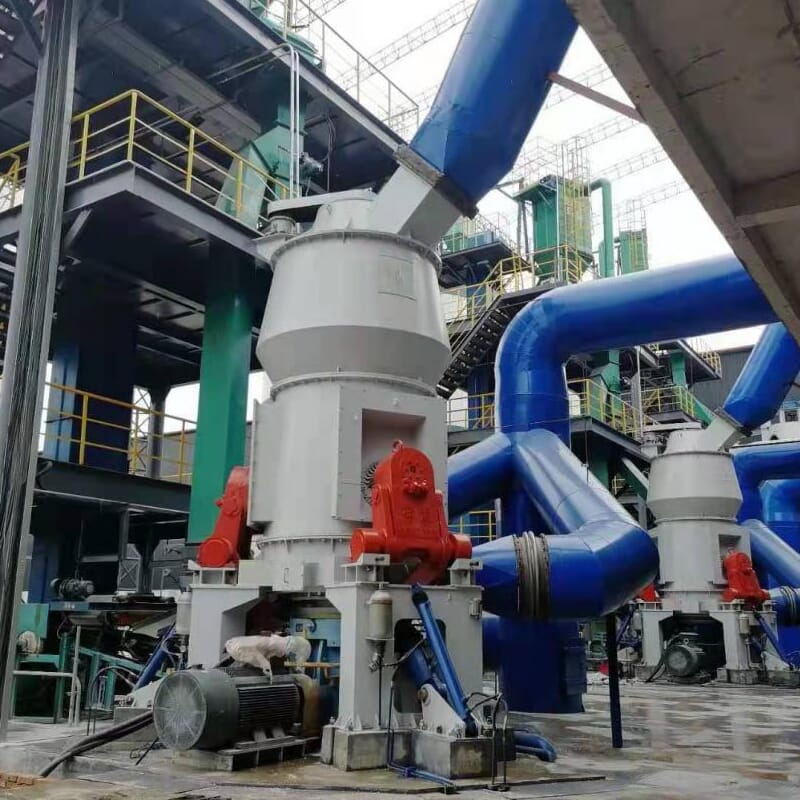
Vertical Roller Mill
Vertical roller mill with a reasonable and reliable structural design,with advanced technological process,set drying, grinding,classifying,improve on the whole,can be precisely the purpose of cutting fineness of 325~2500,with large output, low energy consumption, little pollution of product characteristics.
Vertical roller mill with a reasonable and reliable structural design,with advanced technological process,set drying, grinding,classifying,improve on the whole,can be precisely the purpose of cutting fineness of 325~2500,with large output, low energy consumption, little pollution of product characteristics.
While working, the motor drive the milling disc rotate via gearbox, raw material was fed into milling disc center evenly from the feeding mouth,under the force of centrifugal,the raw material move along the milling disc brim,while go through the ring groove of the milling disc, crushed into powder by the milling rod with grinding pressure, the crushed raw material in the milling disc brim was lifted by the vane high speed airstream, the bigger size will be regrinded by the milling disc once again after falling down, the raw material inside the airstream lift by the airstream. While past through the classifier with high precision above the vertical mill,under the force of high speed rotate rotor,the coarse powder fall down on the mill disc then regrind, the qualified fine powder out of vertical mill, then collect the powder by powder collector then storage in the warehouse or pack directly.
Vertical mill application area: 1. Raw material milling into powder of cement industryo powder of cement industry; 2. Preparation coal ash for different industries,The coal ash fineness can be adjusted according to the product usage; 3. Can be used for power plant desulfurization using limestone powder; 4. Super-grinding mill for various raw materials in non-metallic mineral industry. Equipment parameters of vertical mill FTL vertical roller mill has the following unique characteristics: 1. The grinding roller can be taken out of the mill for maintenance with the help of hydraulic roll turning device, and the vulnerable parts can be replaced to shorten the grinding stop time and improve the operation efficiency. 2. The roller sleeve of grinding roller can be used upside down, which prolongs the service life of wear-resistant materials. 3. There is no need to distribute material on the grinding disc before starting, and the mill can be started without load, so as to avoid the trouble of starting. 4. The grinding roller limit device is adopted to avoid the violent vibration caused by the short working time of the mill. 5. The new grinding roller sealing device is adopted, which makes the sealing more reliable, and there is no need to seal the fan, which further reduces the oxygen content in the mill and has better explosion suppression performance.